Optimizing Storage Solutions with Industrial Warehouse Racking Systems for Enhanced Efficiency
Nov . 07, 2024 21:43
Understanding Industrial Warehouse Racking An Essential Component of Efficient Storage Solutions
In today's fast-paced industrial landscape, efficient space management is more critical than ever. With rising operational costs and increasing demand for streamlined logistics, businesses must adopt effective storage solutions. One of the most essential components in enhancing storage efficiency is industrial warehouse racking systems. These systems are designed to maximize space utilization, improve accessibility, and enhance inventory management within a warehouse environment.
Industrial warehouse racking refers to a variety of systems and frameworks that support the storage of goods in a warehouse. These racks are designed to hold different types of materials and products, ranging from heavy bulk items to smaller, more delicate goods. The most common types of racking systems include selective pallet racking, drive-in and drive-through racking, push-back racking, and pallet flow racking. Each of these systems has its own set of advantages, making them suitable for specific operational needs.
Selective pallet racking is one of the most widely used systems in warehouses. It allows easy access to individual pallets, making inventory management straightforward. Forklifts can easily maneuver throughout the aisles, enabling workers to retrieve and store items quickly. This system is particularly advantageous for businesses with a high variety of products and moderate inventory turnover.
Drive-in racking systems offer a different approach to warehouse storage, allowing for higher density storage by utilizing the depth of the warehouse. In this system, pallets are stored back-to-back in a single row, requiring forklifts to enter the depths of the rack. While this maximizes space efficiency, it can complicate inventory management since accessing a pallet at the back may require moving several others first. This method is ideal for businesses storing large quantities of the same item.
industrial warehouse racking
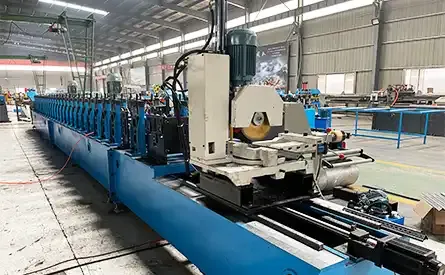
Push-back racking combines elements of both selective and drive-in systems. It allows for higher storage density while still providing access to individual pallets. As goods are loaded onto the racking, they push the previously stored pallets back, allowing easy retrieval from the front. This hybrid approach is suitable for warehouses with moderate variety and demand fluctuations.
Pallet flow racking is another critical method designed for high-throughput operations. This system utilizes gravity to move pallets along inclined tracks, allowing for the first-in-first-out (FIFO) inventory management. As new pallets are loaded from the back, the older pallets are pushed forward, ensuring that stock is rotated regularly. This method is particularly effective for businesses dealing with perishable goods or products with specific expiration dates.
Beyond choosing the right racking system, several factors must be taken into account when designing a warehouse layout. Considerations such as aisle width, load capacity, and safety measures are crucial. Furthermore, regular maintenance of the racking systems is essential to ensure safety and efficiency. Adequate training for warehouse staff on the proper handling and operation of equipment can also significantly enhance operational flow.
In conclusion, industrial warehouse racking systems play a fundamental role in the efficient storage and management of inventory. By understanding the different types of racking systems and their applications, businesses can optimize their warehouse operations, improve accessibility, and ultimately save on costs. As industries continue to evolve, investing in the right racking solutions is not merely beneficial; it is essential for surviving in the competitive market landscape.