perforated mesh screen
Sep . 19, 2024 01:53
The Versatility of Perforated Mesh Screens
Perforated mesh screens are an essential component in a wide range of industrial and architectural applications. Made from various materials such as metal, plastic, or fiberglass, these screens feature a series of holes or openings that provide both functionality and aesthetic appeal. This article explores the benefits, applications, and manufacturing processes of perforated mesh screens.
Key Benefits
One of the primary advantages of perforated mesh screens is their ventilation capability. The strategic distribution of holes allows for air, light, and sound to pass through while maintaining structural integrity. This feature is particularly important in various industries, including HVAC systems, where properly vented systems enhance efficiency and indoor air quality.
Additionally, perforated mesh screens are valuable for filtration purposes. They serve as effective barriers that can separate solids from liquids or gases, making them ideal for use in water treatment plants, food processing, and chemical manufacturing. The precise size and shape of the perforations can be customized to meet the specific needs of the application, ensuring optimal performance.
Diverse Applications
The applications of perforated mesh screens span numerous fields. In construction and architecture, these screens are often utilized as decorative elements in facades, balconies, and partition walls. The patterns created by the perforations can add an artistic touch while providing shade and reducing heat gain, contributing to energy efficiency.
perforated mesh screen
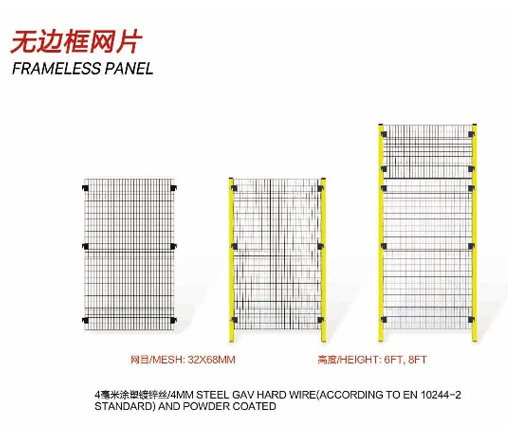
In the manufacturing sector, perforated mesh screens are widely used in machinery, conveyor systems, and safety barriers. Their durability and robustness make them suitable for handling heavy materials while minimizing wear and tear. Furthermore, these screens can be engineered to withstand harsh environmental conditions, enhancing their longevity and reliability.
Manufacturing Process
The manufacturing of perforated mesh screens typically involves several steps. First, a sheet of the chosen material is selected based on the specific requirements of the application. Common materials include stainless steel, aluminum, and plastic. Once the material is chosen, the perforation process begins. This can be done using various techniques, such as punching, laser cutting, or water jet cutting, ensuring precise hole dimensions and spacing.
After the perforation, the screens may undergo additional treatments to enhance their performance. For instance, they can be coated for corrosion resistance or painted for aesthetic purposes. Quality control is critical during this stage, as it ensures that the finished product meets industry standards.
Conclusion
Perforated mesh screens are a versatile solution that combines functionality with aesthetic value across various industries. Their ability to provide ventilation, filtration, and durability makes them indispensable in construction, manufacturing, and beyond. As technology advances, the manufacturing processes for these screens continue to improve, allowing for greater customization and enhanced performance. Whether used in an industrial setting or as part of architectural design, perforated mesh screens are set to play a pivotal role in modern applications.