Innovative Techniques for Joining Plastic Materials Using Welding Mesh Solutions
Déc . 18, 2024 12:38
Understanding Plastic Welding Mesh Applications, Benefits, and Innovations
Plastic welding mesh has emerged as a vital component in various industries, revolutionizing how products are manufactured and assembled. This mesh, characterized by its durability and flexibility, is created through a sophisticated process that involves heat application to fuse plastic materials together. This article explores the applications, benefits, and innovations surrounding plastic welding mesh.
Applications of Plastic Welding Mesh
Plastic welding mesh is widely used in diverse fields such as automotive, construction, agriculture, and packaging. In the automotive industry, it can be utilized for producing components like interior panels, ensuring they are both lightweight and strong. The mesh is integral in manufacturing products that require perforated surfaces, providing ventilation while maintaining structural integrity.
In the construction sector, plastic welding mesh is employed for safety barriers and protective enclosures. This mesh is particularly favorable as it can withstand extreme weather conditions, making it suitable for outdoor applications. Furthermore, its lightweight nature allows for easy transportation and installation, contributing to efficient project timelines.
In agriculture, plastic welding mesh is actively used for creating protective covers for crops, helping to maintain optimal growing conditions while deterring pests. Additionally, its ability to be molded into various shapes and sizes allows farmers to customize solutions for their unique needs.
Benefits of Plastic Welding Mesh
The benefits of plastic welding mesh are manifold. Firstly, it offers excellent strength-to-weight ratios, making products both lightweight and durable. This characteristic is crucial in industries where reducing weight without compromising quality is essential, such as in automotive manufacturing.
plastic welding mesh
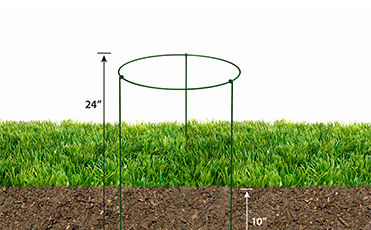
Secondly, plastic welding mesh exhibits exceptional resistance to harsh chemicals and UV radiation. This makes it suitable for outdoor and industrial applications, where exposure to such elements could lead to degradation. As a result, products made with this mesh tend to have a longer lifespan, translating to lower replacement and maintenance costs for businesses.
Moreover, the welding process used to create this mesh allows for a seamless finish, enhancing not only the aesthetic appeal of products but also their functionality. The continuous nature of the welds reduces the risk of failure, as there are no weak points—contrary to products made with conventional fasteners or adhesives.
Innovations in Plastic Welding Mesh
Innovation in plastic welding mesh technology has been profound, driven by the increasing demand for sustainable and efficient production practices. New techniques, such as ultrasonic welding and laser welding, have improved the precision and speed of the welding process. These advancements minimize energy consumption and waste, aligning with contemporary sustainability goals.
Additionally, the introduction of bio-based plastics into the welding process represents another significant innovation. By utilizing renewable resources, manufacturers are not only reducing their carbon footprint but also appealing to environmentally conscious consumers.
Moreover, the integration of smart technologies, such as IoT (Internet of Things) sensors in plastic welding mesh manufacturing, enhances quality control. Real-time monitoring systems can now track the welding process, ensuring that each product meets the required standards and specifications.
Conclusion
In summary, plastic welding mesh is a critical player in modern manufacturing and construction paradigms. Its diverse applications, coupled with significant benefits like strength, resilience, and an aesthetically pleasing finish, have made it indispensable across various sectors. As innovations continue to emerge, including sustainable practices and advanced welding technologies, the future of plastic welding mesh looks promising. Industries that adopt these advancements stand to gain competitive advantages, reducing costs while enhancing product quality, ultimately shaping a more efficient and eco-friendly industrial landscape.