A similar title inspired by 30% 20 mesh for industrial applications
Dec . 31, 2024 20:20
Understanding 30% 20 Mesh A Key Component in Material Engineering
In the realm of material engineering and manufacturing processes, the term mesh is often employed to describe the size of particles, typically in the context of powders or granular materials. One specific classification that frequently arises is 30% 20 mesh. This phrase encapsulates both a sizing specification and a crucial quality indicator that experts utilize in various industries, from pharmaceuticals to construction.
What Does 30% 20 Mesh Mean?
To dissect the term, we first need to understand what 20 mesh signifies. Mesh size refers to the number of holes per linear inch in a sieve or screen. For example, a 20 mesh screen has 20 openings per inch. This classification indicates that particles that pass through this screen have a nominal size of approximately 0.841 mm (or 841 microns), while particles that are retained are larger than this dimension. The term 30% further specifies that 30% of the particles in the overall mixture fall within this 20 mesh size range.
Importance in Different Industries
The significance of the 30% 20 mesh classification can be observed across various sectors
1. Pharmaceuticals In the pharmaceutical industry, particle size directly influences the dissolution rate of active ingredients. A controlled distribution of particle sizes, evidenced by a specification like 30% 20 mesh, allows for enhanced bioavailability of drugs. This balance ensures that the medication is efficient and can be absorbed effectively by the body.
2. Construction Materials When it comes to construction, materials' mesh sizes are critical in mixtures like concrete or asphalt. A specification of 30% 20 mesh can imply the ideal particle size distribution that optimizes strength and durability. By carefully calibrating the ratios, engineers create products that meet stringent safety and performance standards.
3. Cosmetics In the cosmetics industry, the texture and application of products are greatly influenced by the particle sizes used. A 30% 20 mesh specification can contribute to the feel and efficacy of products, ensuring a smooth application while maintaining the desired bonding and skin adherence properties.
30 mesh
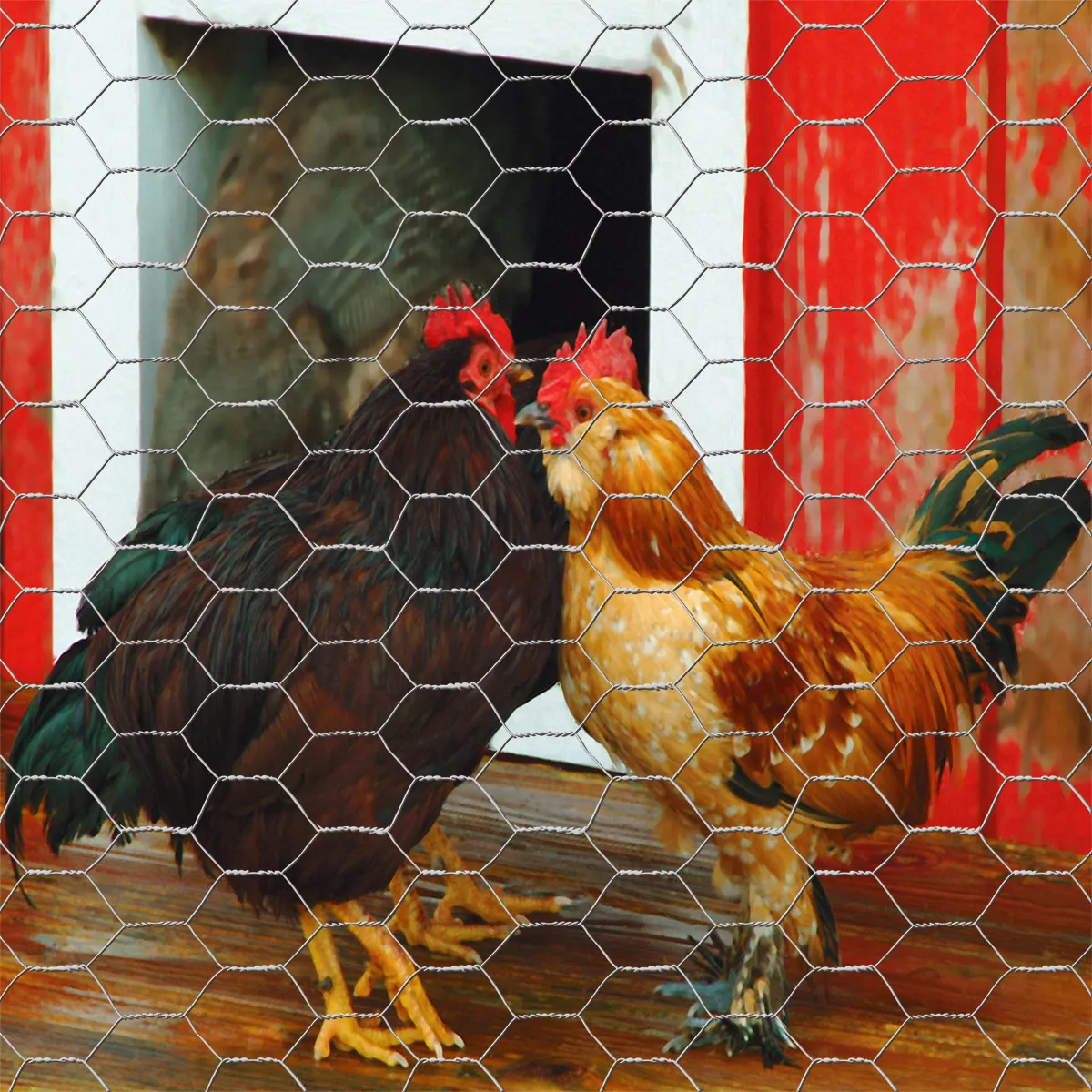
The Process of Achieving the Right Mesh Size
To achieve a consistent 30% 20 mesh distribution, manufacturers apply several techniques, including sieving, milling, and blending.
- Sieving A common technique where materials are separated based on size using mesh screens. This method ensures that only particles of a desired size remain in the final mixture.
- Milling Involves reducing the size of powders using mechanical means. Different types of mills can produce particles that fit within the 20 mesh classification, allowing for the creation of homogeneous mixtures.
- Blending After achieving the right particle sizes, manufacturers often blend various powders to achieve the final composition that meets the 30% criteria effectively. This step is crucial to ensuring that the material possesses the desired properties, such as flowability or compressibility.
Challenges and Considerations
While the 30% 20 mesh specification provides clear guidance, achieving and maintaining this balance can be challenging. Variability in raw material quality, differences in processing methods, and environmental factors can all affect consistency. Repeatability is essential; hence routine testing and quality control measures are vital to ensure that materials meet the specified parameters.
Conclusion
The concept of 30% 20 mesh exemplifies the delicate balance of particle sizing in material science. From enhancing medication efficacy in pharmaceuticals to ensuring the durability of construction materials, this specification plays a pivotal role in various applications. Understanding and controlling this aspect of material properties can lead to significant advancements in product performance and reliability. As industries continue to innovate, the importance of precise specifications like 30% 20 mesh will only grow, driving the need for improved techniques and technologies in material engineering.