8d common
Dec . 21, 2024 20:44
Understanding the 8D Problem-Solving Methodology
The 8D problem-solving methodology is a structured approach developed to address chronic and systemic problems in various industries, particularly in manufacturing and automotive sectors. The acronym 8D stands for Eight Disciplines, which encapsulates the steps taken to identify, analyze, and resolve issues effectively. This article explores the significance of the 8D process, its eight disciplines, and its overarching role in continuous improvement.
The Significance of 8D
In today’s competitive landscape, organizations continually face challenges that require systematic problem-solving techniques. The 8D methodology not only facilitates a deeper understanding of issues but also encourages collaboration among team members. By breaking down problems into manageable parts, the 8D approach promotes thorough analysis and ensures that solutions are not merely temporary fixes but sustainable remedies.
The Eight Disciplines
1. D1 Establish the Team The first step involves gathering a cross-functional team with the necessary expertise to tackle the problem. A diverse team provides different perspectives and ensures a holistic approach.
.
3. D3 Develop Interim Containment Actions Before solutions are implemented, it is important to devise temporary measures to mitigate the impact of the problem on customers. This allows for immediate relief while long-term solutions are developed.
8d common
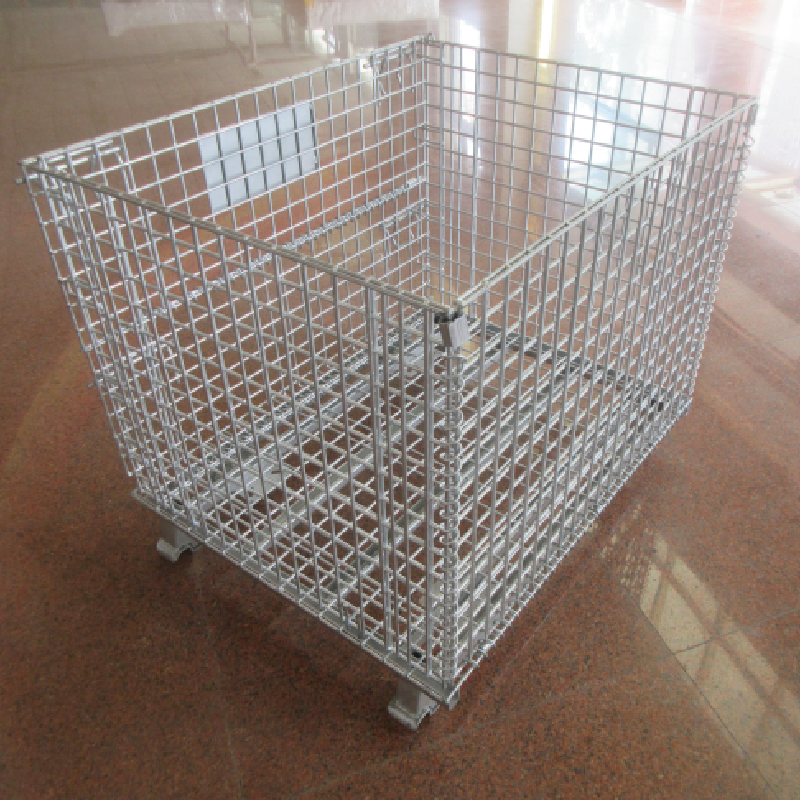
4. D4 Determine Root Causes This step involves thoroughly investigating the problem to uncover its root causes. Techniques such as the 5 Whys and Fishbone Diagrams are often employed to facilitate this analysis. Identifying root causes ensures that solutions address the underlying issues rather than the symptoms.
5. D5 Choose and Verify Permanent Corrections (PCs) After identifying root causes, teams brainstorm and evaluate possible permanent corrective actions. It is essential that these actions are feasible and that their effectiveness is verified through testing before full implementation.
6. D6 Implement Corrective Actions Once permanent solutions are validated, they should be implemented. This may involve changes to processes, technology, or training. Effective communication during this stage is vital to ensure all stakeholders are aware of the new methods.
7. D7 Prevent Recurrence To prevent the problem from recurring, it is essential to modify related systems and processes. Documentation of the findings and corrective actions ensures that lessons learned are captured for future reference.
8. D8 Recognize the Team and Celebrate Success Acknowledging the efforts and successes of the team not only boosts morale but also fosters a culture of continuous improvement. Celebrating achievements reinforces the value of teamwork and encourages engagement in future problem-solving endeavors.
Conclusion
The 8D problem-solving methodology offers a robust framework for addressing complex issues that organizations encounter. By following its structured approach, teams can effectively identify root causes and implement long-lasting solutions, ultimately leading to enhanced efficiency, improved product quality, and heightened customer satisfaction. In an era where operational excellence is paramount, mastering the 8D process is an invaluable skill for professionals across various industries. Whether tackling minor defects or significant systemic issues, the discipline of 8D fosters a proactive mindset, making it a vital tool for sustained organizational success.