Nails Used for Proper Installation of Lead Flashing in Roofing Projects
Oct . 10, 2024 07:53
Understanding Nails for Lead Flashing A Comprehensive Guide
Lead flashing is an essential component in roofing that prevents water from penetrating vulnerable areas, such as joints and seams. Proper installation of lead flashing is crucial to ensure durability and effectiveness. A key aspect of this installation is the use of nails, and understanding the types and applications of nails suited for lead flashing can significantly impact the longevity of your roofing system.
When considering nails for lead flashing, the first factor to keep in mind is the material of the nails. Corrosion resistance is vital since lead flashing is often exposed to the elements. Traditionally, galvanized nails have been popular due to their zinc coating, which protects against rust. However, for better long-term durability, stainless steel nails are increasingly recommended. They provide superior corrosion resistance, making them ideal for environments with high moisture levels or exposure to salt—common in coastal areas.
The length and gauge of the nails are also critical factors. Nails should be long enough to penetrate the underlying layer securely without excessive protrusion, which can lead to water pooling. Generally, a nail length of 1.5 to 2 inches is suitable for most lead flashing applications, with a gauge of 10 or 12 commonly used. Thicker nails provide more holding power, which is essential for maintaining the integrity of the flashing over time.
nails for lead flashing
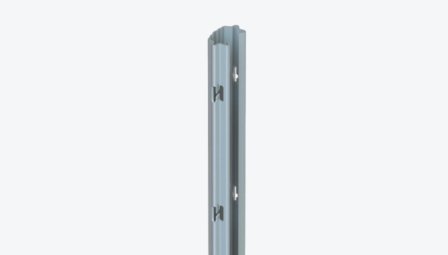
The installation process is crucial when using nails for lead flashing. It is recommended to use at least one nail every 12 inches along the top edge of the flashing. Additionally, nails should be placed about 1 inch away from the edge of the lead to avoid tearing or distorting the material. It's important to avoid over-driving the nails, which can cause damage to the flashing and lead to leaks. Instead, nails should be snugly driven in, allowing for a slight but effective sealing by the flashing material itself.
Moreover, the placement of the nails can affect the performance of the lead flashing. For areas with significant water flow, such as valleys or roof intersections, additional fastening might be necessary to maintain the flashing's position against the force of the water. In such cases, using special lead cleats, which are small nails or clips designed specifically for holding lead flashing, can provide extra security.
Another essential consideration is ensuring that the flashing overlaps adequately with other roofing materials, such as shingles or tiles. The overlap should be at least 4 inches to ensure proper drainage and to minimize the risk of water penetration beneath the flashing. When securing the flashing, care should be taken that the nails do not obstruct this overlap but adequately hold the flashing in place.
In conclusion, selecting the right nails for lead flashing installation is a foundational aspect of effective roofing. Using corrosion-resistant materials, appropriate lengths and gauges, and following correct installation practices can significantly enhance the performance and longevity of lead flashing. Whether you are a seasoned roofer or a DIY enthusiast, understanding these principles will help in creating a waterproof and durable roofing solution that stands the test of time. Always consult with professionals if uncertain, as proper installation can save time, money, and headaches in the long run.