Racking Shelves for Warehouse Optimization
Sep . 07, 2024 11:57
Efficient Racking Systems for Warehouse Shelving A Guide
In the fast-paced world of logistics and warehousing, the proper organization of goods is vital for operational efficiency. One of the most critical aspects of warehouse management is the racking or shelving system employed to store products. An effective racking system not only maximizes space but also enhances productivity, safety, and accessibility. This article explores various types of racking systems and their advantages, helping warehouse managers choose the best solution for their needs.
Types of Racking Systems
1. Selective Pallet Racking
Selective pallet racking is perhaps the most common racking system used in warehouses. It consists of vertical frames and horizontal beams that create individual shelves for pallets. This type of racking provides easy access to each pallet, allowing for the efficient picking of goods. It is ideal for warehouses that need to store a variety of items, as it can accommodate different pallet sizes and is flexible enough to adjust to changing inventory levels.
2. Drive-In Racking
Drive-in racking is designed for high-density storage. It allows forklifts to drive directly into the racking system, maximizing vertical space while minimizing the aisle width. This method is particularly useful for storing large quantities of similar products, as it operates on a last in, first out (LIFO) basis. However, careful inventory management is required to ensure ease of access and rotation.
Cantilever racking is specialized for storing long and bulky items, such as lumber or pipes. It features arm-like extensions that allow goods to be loaded from either side without the need for A-frames. This racking system is easily adjustable, making it a versatile option for warehouses that handle various lengths and sizes of inventory.
4. Mobile Racking
racking shelves for warehouse
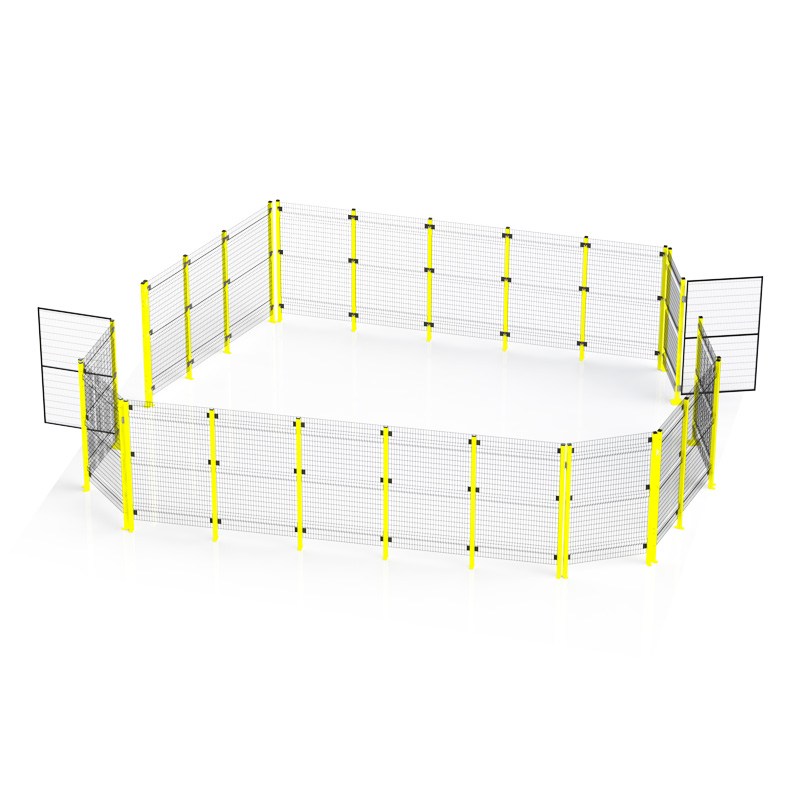
Mobile racking systems are designed to maximize space by utilizing mobile bases that can move along tracks. This configuration allows for the elimination of fixed aisles, permitting more racks in the same area. Mobile racking is especially beneficial for cold storage environments, where space is always at a premium, and quick access to goods is essential.
Choosing the Right Racking System
When selecting an appropriate racking system, warehouse managers should consider several factors
- Inventory Type Analyze the types of products to be stored. For diverse inventories, selective or multi-tier racking systems may be advantageous. For uniform stock, high-density systems like drive-in or mobile racking may provide better space utilization.
- Space Availability Assess the warehouse layout and available height. If vertical space is ample, taller racking systems can increase capacity without requiring additional floor space.
- Accessibility Needs Determine the picking and replenishing processes. Systems that offer easy access, such as selective racking, may facilitate faster operations.
- Budget Considerations Evaluate the initial costs versus the long-term benefits of various racking options. While high-density solutions may require higher upfront investments, they could lead to cost savings through improved efficiencies.
Conclusion
Selecting the right racking system for warehouse shelving is crucial for optimizing operations. By understanding the various types of racking systems available and considering the specific needs of the warehouse, managers can establish an efficient, organized, and flexible storage solution. Ultimately, well-implemented racking systems contribute to enhanced productivity and streamlined operations, paving the way for a successful warehousing strategy.