roofing nails for underlayment
Dec . 03, 2024 18:17
Understanding Roofing Nails for Underlayment A Comprehensive Guide
When it comes to roofing, one of the most critical components that ensure durability and performance is the underlayment. This protective layer serves as a barrier against water infiltration and acts as a cushion, safeguarding the roofing material and the home's interior. However, the effectiveness of roofing underlayment largely depends on the quality of roofing nails used in the installation process. This article delves into the importance of roofing nails, their types, and best practices for securing underlayment.
What is Underlayment?
Underlayment is a material placed between the roof deck and the roofing material, such as shingles or tiles. Typically made from felt paper or synthetic materials, underlayment offers an additional layer of protection against water, wind, and ice. Depending on the type of roofing material being used, the underlayment can vary, but its fundamental purpose remains the same to act as a barrier that prevents moisture from penetrating into the roof structure.
The Role of Roofing Nails
Roofing nails are essential for fastening underlayment to the roof deck. They must be chosen carefully to ensure that they hold the underlayment securely in place and withstand the rigors of weather conditions. The integrity of the entire roofing system can be compromised if the underlayment is not properly attached due to inadequate or inappropriate nails.
Types of Roofing Nails
1. Galvanized Steel Nails These nails are coated with zinc to prevent rust and corrosion, making them suitable for use in various weather conditions. They are the most common type of nails used in roofing applications.
2. Stainless Steel Nails While more expensive, stainless steel nails provide superior resistance to rust and corrosion. They are ideal for coastal areas where salt exposure can hasten the deterioration of metal.
3. Plastic Cap Roofing Nails These nails feature a plastic cap that provides additional support and helps to prevent the underlayment from tearing. They are particularly useful in high-wind regions.
roofing nails for underlayment
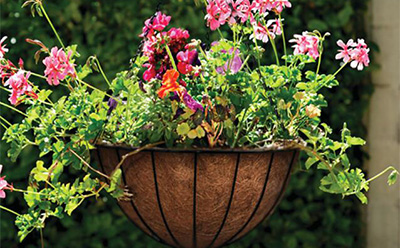
4. Copper Nails Although they are less commonly used, copper nails are highly resistant to corrosion and are often employed in historical restoration projects or high-end applications.
Best Practices for Using Roofing Nails with Underlayment
1. Choose the Right Size The standard roofing nail length for underlayment is typically 1 to 1.5 inches. Ensure that the nail length is adequate to penetrate through the underlayment and into the roof deck without compromising structural integrity.
2. Proper Spacing Nail spacing is crucial for ensuring that the underlayment is secured effectively. It is generally recommended to space nails about 12 inches apart in a staggered pattern. This distribution provides even support and reduces the likelihood of water infiltration.
3. Avoid Overdriving Overdriving nails can cause damage to the underlayment and may lead to water leaks. It’s essential to maintain a flush surface where the nail head is just below the underlayment surface without puncturing it.
4. Inspect for Damage After installation, inspect the underlayment to ensure that no damage has occurred during the nailing process. Look for any tears or irregularities that could compromise the waterproofing abilities of the underlayment.
5. Follow Manufacturer Guidelines Always refer to the manufacturer’s specifications regarding nail types, lengths, and installation practices. Adhering to these guidelines will help ensure compliance with warranty requirements and industry standards.
Conclusion
The right roofing nails are vital for the effective installation of underlayment, which plays a crucial role in protecting your roofing system. By choosing the appropriate materials and following best practices, homeowners and roofing professionals can ensure that their roofs withstand the test of time and environmental challenges. Ultimately, diligent attention to detail during the installation process will yield a durable and reliable roofing system that serves its purpose for years to come.