Understanding the Expenses Associated with Warehouse Shelving and Storage Solutions for Businesses
Aug . 11, 2024 00:40
Understanding Warehouse Shelving Costs An Essential Guide for Warehouse Management
Effective warehouse management is pivotal for businesses that rely on efficient logistics and inventory management. One critical aspect that significantly influences overall operational efficiency is the cost associated with warehouse shelving. This article aims to provide a comprehensive overview of the factors affecting warehouse shelving costs, helping businesses make informed decisions when designing their storage solutions.
The Importance of Warehouse Shelving
Warehouse shelving plays a crucial role in maximizing storage space and improving accessibility to goods. Properly designed shelving can streamline operations, enabling quicker picking and restocking processes. Investing in the right shelving solutions can lead to increased productivity, reduced labor costs, and better utilization of warehouse space. However, understanding and managing shelving costs is vital for maintaining budget constraints while achieving operational effectiveness.
Factors Influencing Warehouse Shelving Costs
1. Type of Shelving The type of shelving selected is one of the most significant contributors to cost. Common shelving types include selective racking, drive-in racking, pallet flow racking, and cantilever racking. Each type has varying price points based on material, design complexity, and load-bearing capacities. For instance, a selective racking system, though more cost-effective, may not maximize vertical storage compared to pallet flow racking, which often comes at a higher price.
2. Material Quality Shelving systems are constructed from various materials, such as steel, plastic, or wood. Steel shelving is typically more durable and able to support heavier loads, making it a more expensive option. The investment in high-quality materials may lead to lower maintenance costs and a longer lifespan, which can justify the higher initial expenditure.
warehouse shelving cost
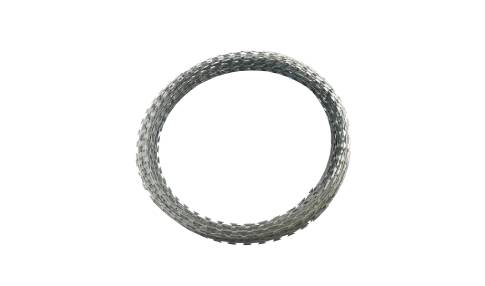
3. Customization and Design Custom-built shelving solutions tailored to specific warehouse needs can significantly increase costs. While off-the-shelf options may be cheaper, they might not optimize storage efficiency as effectively as bespoke designs. Organizations should weigh the benefits of custom solutions against their budget constraints.
4. Installation and Labor Costs The expenses associated with installing shelving can often be overlooked. Depending on the complexity of the shelving system, labor costs can vary. Some forms of shelving may require professional installation, which can add to the overall cost. In contrast, simpler systems might allow for self-installation, saving on labor expenses.
5. Maintenance and Longevity The long-term costs associated with shelving should also be considered. Over time, wear and tear can lead to maintenance expenses or even the need for replacement. Investing in durable and resilient shelving materials can minimize these long-term costs, making it a smart financial choice.
6. Warehouse Layout The layout of the warehouse affects shelving design and costs. An efficient layout maximizes storage space but may require a complex shelving solution that could be more expensive. Conversely, a poorly designed layout can lead to higher operational costs and wasted space.
Conclusion
Understanding warehouse shelving costs is essential for effective warehouse management. By carefully considering the type of shelving, material quality, customization options, installation costs, and maintenance requirements, businesses can make informed choices that balance cost and efficiency. Investing in the right shelving solutions not only enhances storage capacity and operational efficiency but can also lead to long-term savings. As the logistics and warehousing sectors continue to evolve, staying mindful of shelving costs and their implications can provide a competitive edge in an increasingly dynamic marketplace.