warehouse inventory shelving
Sep . 26, 2024 06:26
Optimizing Warehouse Inventory Shelving Strategies for Efficiency and Accessibility
In today’s fast-paced supply chain environment, efficient inventory management is crucial for ensuring that goods move smoothly from suppliers to customers. One of the key elements in this process is the design and organization of warehouse inventory shelving. Proper shelving not only maximizes space but also enhances accessibility and reduces the time workers spend locating and retrieving items. This article explores effective strategies for optimizing warehouse inventory shelving.
Understanding Warehouse Shelving
Warehouse shelving refers to the various types of structures used to store products in a warehouse environment. These systems can range from simple racks to complex automated shelving units. The primary goal of any shelving system is to maximize vertical and horizontal space while allowing easy access to inventory items.
Key Considerations for Shelving Design
1. Space Utilization One of the foremost considerations in shelving design is space utilization. Warehouses often have high ceilings, which means upward space can be used effectively. Racking systems that reach higher allow for more inventory to be stored without needing additional floor space. However, it is essential to balance height with accessibility. Workers should be able to safely reach stored items.
2. Inventory Classification Different types of items require different shelving solutions. Classifying inventory into categories such as fast-moving goods, slow-moving items, and seasonal products can aid in deciding how they should be stored. Fast-moving items should be kept on accessible shelves closer to the shipping area, while slower-moving items can be stored higher or further from the picking zones.
3. Modular Shelving Systems Implementing modular shelving systems allows for flexibility in warehouse layout. These systems can be configured and reconfigured as inventory needs change, accommodating varying product sizes and volumes. This adaptability is crucial in a dynamic market where demand can shift unexpectedly.
4. Ergonomics and Accessibility Shelving systems must also prioritize ergonomics to minimize strain on workers. The height of shelves should consider the average worker's reach. Additionally, designing aisles for easy movement can alleviate bottlenecks during picking and packing processes. The use of mobile shelving units can lead to increased efficiency, allowing workers to have items within easy reach without excessive bending or stretching.
warehouse inventory shelving
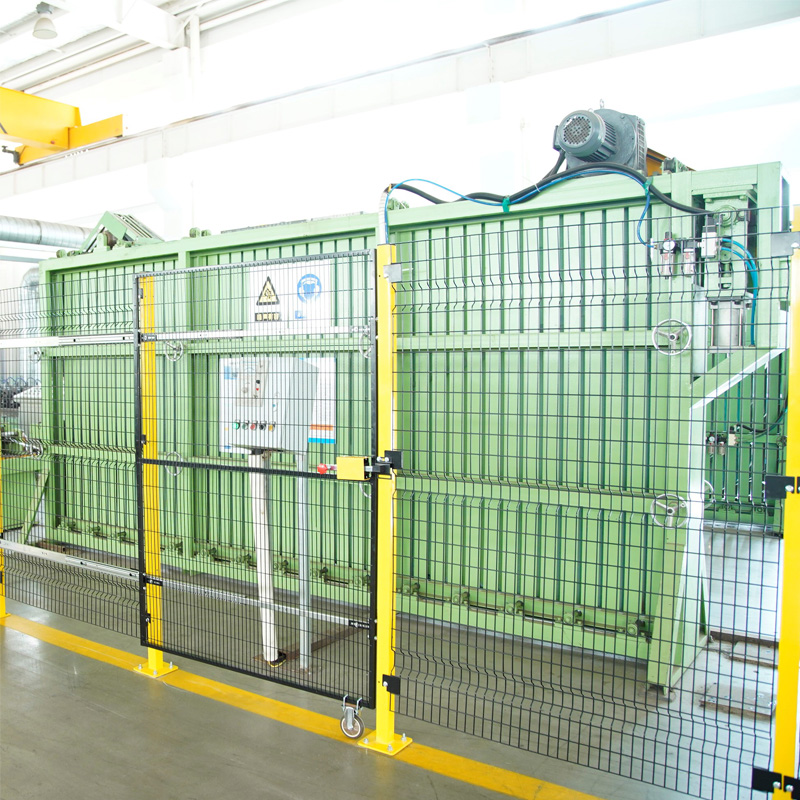
5. Technology Integration The integration of technology can significantly enhance shelving efficiency. Warehouse Management Systems (WMS) can track inventory levels and locations in real-time, allowing for better organization and quick retrieval. Automated shelving and retrieval systems can further streamline processes, reducing the manual labor needed to manage inventory.
Best Practices for Inventory Shelving
1. Regular Auditing Conduct regular audits of shelving practices to ensure they remain efficient. This can involve checking for any obsolete items taking up valuable space and reassessing the organization of frequently accessed items.
2. Cross-docking Consider employing a cross-docking approach if applicable. This system minimizes storage time by transferring items directly from incoming to outgoing shipping, reducing the need for extensive shelving.
3. Implement FIFO or LIFO Practices Depending on the nature of your products, implementing First In, First Out (FIFO) or Last In, First Out (LIFO) practices can help manage inventory effectively. FIFO is crucial for perishable goods, while LIFO might be suitable for certain manufactured products.
4. Employee Training Educate employees on the importance of maintaining organized shelving practices. Training staff on how to retrieve and store items correctly ensures that the shelving system remains efficient and reduces the chances of errors.
Conclusion
Optimizing warehouse inventory shelving is a multifaceted challenge that requires careful consideration of various factors, including space utilization, inventory classification, ergonomic design, and technology integration. By adopting best practices and continually assessing shelving systems, businesses can enhance their operational efficiency, reduce costs, and improve overall inventory management. As the warehouse landscape continues to evolve, so too must the strategies employed to ensure that shelving remains an asset rather than a liability. Efficient shelving is not just about storing items; it plays a crucial role in the broader logistics and supply chain process, affecting everything from order fulfillment to customer satisfaction.