Efficient Warehouse Shelving Solutions for Optimized Order Picking Processes
11 月 . 28, 2024 07:14
Optimizing Warehouse Picking Shelves for Efficiency
In today’s fast-paced logistics environment, the efficiency of warehouse operations is a crucial factor that can significantly impact overall business performance. One of the key components contributing to this efficiency is the design and organization of picking shelves within a warehouse. Optimizing warehouse picking shelves not only enhances order fulfillment speed but also helps in reducing operational costs and improving customer satisfaction.
Understanding Picking Shelves
Picking shelves are specialized storage systems used in warehouses where items are stored and easily retrieved to fulfill customer orders. These shelves are strategically organized to facilitate quick access to products, ensuring that warehouse staff can pick items swiftly and accurately. The design of these picking systems can vary greatly, depending on the type of products being handled, the volume of orders, and the specific needs of the business.
Importance of Shelf Organization
Proper organization of picking shelves is essential for several reasons. Firstly, it minimizes the time workers spend searching for items. A well-organized picking area can lead to significantly reduced travel time, allowing employees to retrieve items quickly. Secondly, good shelf organization helps in maintaining inventory accuracy. When products are stored in designated locations, the chances of mispicks and errors decrease, resulting in fewer returns and increased customer satisfaction.
Strategies for Optimizing Picking Shelves
To maximize the efficiency of picking shelves, businesses can implement several strategies
warehouse picking shelves
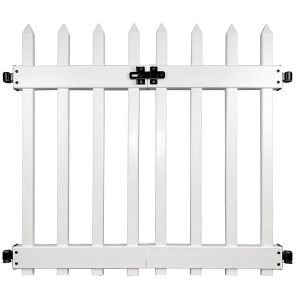
1. ABC Classification This inventory management technique involves categorizing items based on their importance and sales frequency. 'A' items are the most valuable and frequently sold, while 'C' items are the least. By placing high-volume items closer to the packing and shipping areas, warehouses can reduce travel time and increase picking speed.
2. Ergonomic Design Designing picking shelves that are easy to access can lead to significant productivity gains. Shelves should be at a height that reduces the need for stretching or bending and can facilitate the use of equipment like pick carts or forklifts. User-friendly design also prevents worker fatigue, promoting a safer working environment.
3. Dynamic Slotting Dynamic slotting refers to the practice of regularly rearranging inventory based on changes in demand. By continuously monitoring sales data, warehouses can move fast-selling items to more accessible locations, ultimately improving picking efficiency.
4. Utilizing Technology The integration of technology such as barcode scanners, RFID systems, and warehouse management software can vastly improve the picking process. These tools assist in tracking inventory levels in real-time and help workers identify the fastest routes to pick items, thereby reducing errors and ensuring quicker fulfillment.
5. Regular Training and Evaluation Continuous training of warehouse staff should not be overlooked. Employees should be well-versed in the layout of the picking shelves and any technology used during the picking process. Regular evaluations of both the shelving system and staff efficiency can identify areas for improvement.
Conclusion
In conclusion, the efficiency of warehouse picking shelves plays a vital role in the overall performance of warehouse operations. By implementing thoughtful strategies such as ABC classification, ergonomic design, dynamic slotting, and technological integration, businesses can significantly enhance their picking processes. A well-organized and efficiently utilized picking shelf system not only maximizes productivity but also contributes to higher customer satisfaction and ultimately drives business success. In an era where every second counts, optimizing warehouse picking shelves is not just an operational necessity but a competitive advantage.