wire mesh screen
11 月 . 21, 2024 01:56
The Essential Guide to Wire Mesh Screens Versatility and Applications
Wire mesh screens are an essential component across a multitude of industries, providing effective solutions for filtration, separation, and support. Their functionality arises from the intricate design and construction of the mesh, made from metals such as stainless steel, aluminum, and brass, allowing them to withstand a variety of conditions. This article will explore the types, applications, manufacturing processes, and advantages of wire mesh screens, emphasizing their significance in modern industry.
Types of Wire Mesh Screens
Wire mesh screens come in various types, categorized mainly by their weave patterns, material, and wire diameter. The most common weave patterns include plain weave, twill weave, and Dutch weave.
1. Plain Weave This is the most basic and widely used type. It is created by weaving the warp (vertical wires) and weft (horizontal wires) at right angles, providing a balanced structure suitable for basic filtration and support.
2. Twill Weave This involves a more complex interlacing pattern that produces a denser mesh. Twill weave screens offer increased strength and durability, making them ideal for more demanding applications.
3. Dutch Weave In this variation, the wire diameter of the warp is heavier than that of the weft. This creates a tighter mesh that is particularly effective for fine filtration applications, commonly used in the petrochemical and food processing industries.
Manufacturing Processes
The production of wire mesh screens involves multiple steps, beginning with selecting the right raw materials. High-quality stainless steel is often preferred for its corrosion resistance and durability. The manufacturing process typically includes the following stages
- Wire Drawing This involves reducing the diameter of the wire by pulling it through a series of dies, ensuring the required thickness is achieved.
- Weaving The drawn wire is then woven into mesh according to the specified pattern, which can be done using automated machinery for precision and efficiency.
- Finishing After weaving, the mesh may be treated with various coatings (like galvanization or plastic coating) to enhance its corrosion resistance and longevity.
wire mesh screen
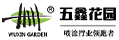
- Cutting and Framing Finally, the mesh is cut to size and may be framed, depending on its intended use. Custom sizes and shapes can be manufactured based on client specifications.
Applications of Wire Mesh Screens
The versatility of wire mesh screens allows for extensive use across numerous fields
- Industrial Filtration In oil and gas industries, wire mesh is vital for separating solids from liquids. It is also used in water treatment facilities to filter out particulate matter.
- Construction Wire mesh screens serve as reinforcement in concrete construction, providing stability and strength. They are also used in fencing and security applications.
- Agriculture Farmers utilize wire mesh to create barriers for crops, support growth, and control pests. It also plays a role in soil erosion prevention techniques.
- Automotive Wire mesh screens are employed in air filters, oil filters, and various other components in vehicles, ensuring proper functionality and safety.
Advantages of Wire Mesh Screens
The use of wire mesh screens presents numerous benefits. Their high durability and resistance to wear and tear make them suitable for long-term use. The open structure allows for successful fluid or air passage, making them ideal for filtration applications. Additionally, wire mesh screens are customizable, meaning they can be tailored to specific dimensions and mesh sizes to meet unique industry requirements.
Moreover, wire mesh screens are cost-effective due to their longevity and low maintenance needs. They can withstand harsh environmental conditions, including high temperatures and corrosive substances, which enhances their appeal in demanding applications.
Conclusion
In summary, wire mesh screens are invaluable tools that serve a wide array of functions across various industries, from filtration and separation to reinforcement and security. Their unique manufacturing processes, versatility, and durability contribute to their essential role in modern technological and industrial applications. As industries continue to evolve and demand more advanced solutions, wire mesh screens will undoubtedly remain a pivotal component in a plethora of sectors.