welding axle spindles
9月 . 22, 2024 19:22
The Importance of Welding Axle Spindles in Automotive Applications
Welding axle spindles represents a critical aspect of automotive manufacturing and repair, playing a significant role in vehicle performance, safety, and overall durability. Axle spindles are integral components that connect the vehicle's wheels to the axle and provide stability during operation. The process of welding these spindles is essential for ensuring they can withstand the stresses and strains encountered during driving.
Understanding Axle Spindles
Axle spindles serve multiple purposes; they support the weight of the vehicle, enable the wheels to rotate smoothly, and facilitate steering in front-wheel drive systems. The design and construction of these components are paramount, as they must endure various forces, including acceleration, braking, and turning. Any failure in the spindle can lead to serious consequences, including vehicle instability and accidents.
The Welding Process
Welding is a fabrication process that joins materials, usually metals or thermoplastics, through the application of heat, pressure, or both. In the context of axle spindles, welding is employed to attach different parts of the spindle assembly, ensuring a robust and resilient structure.
The most common welding techniques used in this application include MIG (Metal Inert Gas) and TIG (Tungsten Inert Gas) welding. MIG welding is favored for its speed and efficiency, making it suitable for high-volume production, while TIG welding provides a cleaner, more precise weld suitable for intricate work and thicker materials.
Benefits of Welding Axle Spindles
welding axle spindles
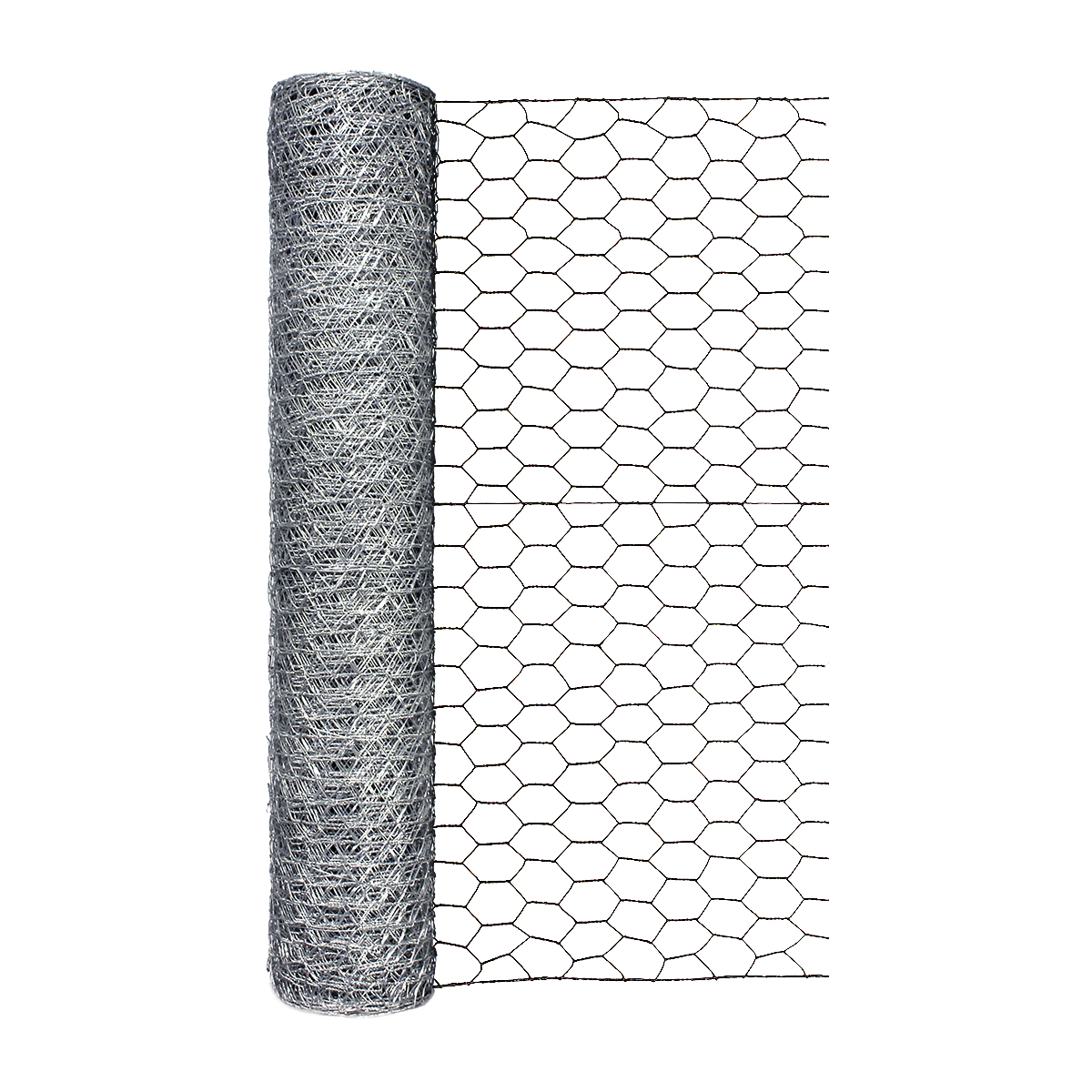
1. Strength and Durability Proper welding techniques enhance the strength of axle spindles, making them capable of handling heavy loads and harsh driving conditions. A well-welded spindle can significantly extend the lifespan of a vehicle's suspension system.
2. Improved Safety Properly welded spindles contribute to overall vehicle safety. A failure in this component can lead to wheel detachment, loss of control, or accidents. Ensuring the integrity of spindles through quality welding prevents such catastrophic failures.
3. Cost-Effectiveness While welding requires an upfront investment in skilled labor and equipment, it often results in lower long-term costs. The durability gained through quality welding reduces the frequency of repairs and replacement, ultimately saving money for manufacturers and consumers alike.
4. Customization Welding allows for customization of axle spindles to meet the specific needs of different vehicle models or aftermarket modifications. This flexibility enables automotive manufacturers to cater to various market segments, from standard family cars to high-performance vehicles.
Challenges in Welding Axle Spindles
Despite its benefits, welding axle spindles is not without challenges. Issues such as distortion during the welding process, potential heat-affected zones, and the need for precise alignment can complicate production. Additionally, selecting the right materials and welding techniques is crucial to achieve the desired strength and performance.
Conclusion
Welding axle spindles is a vital process in the automotive industry that ensures safety, durability, and performance. As vehicles continue to evolve with advanced technologies and materials, the welding techniques used to fabricate these critical components must also adapt. Continuous training for welders, investment in modern equipment, and the application of innovative welding techniques will ensure that future vehicles remain safe and reliable. Ultimately, the importance of well-welded axle spindles cannot be overstated, as they are key to the performance and safety of modern vehicles.