Innovative Solutions for Efficient Pallet Warehouse Storage and Racking Systems
Nov . 10, 2024 02:35
Understanding Pallet Warehouse Racking Key Insights
In the realm of modern logistics and warehousing, efficiency and organization play crucial roles in ensuring smooth operations. One of the most essential components that contribute to this efficiency is pallet warehouse racking. This system not only optimizes space but also enhances accessibility and simplifies inventory management. In this article, we delve into the various aspects of pallet warehouse racking, exploring its types, benefits, and best practices for implementation.
What is Pallet Warehouse Racking?
Pallet warehouse racking refers to a storage system designed to support products stored on pallets in a warehouse. These racks are typically made from steel and can hold various weights depending on their design and configuration. The primary purpose of pallet racking is to maximize the usable space within a warehouse, allowing businesses to store more goods in a limited area while maintaining efficient access to products.
Types of Pallet Racking Systems
There are several types of pallet racking systems available, each catering to different storage needs and warehouse layouts
1. Selective Pallet Racking This is one of the most common and versatile types of racking. It allows access to every pallet stored, making it ideal for warehouses with a wide variety of products. Selective racking systems utilize horizontal beams to store pallets at various levels.
2. Drive-In Racking This system allows forklifts to drive into the rack to access pallets. It is suitable for high-density storage of homogeneous products, significantly maximizing storage capacity.
3. Push Back Racking In this system, pallets are loaded onto a series of wheeled carts that push the pallets back as new pallets are loaded. This allows for efficient use of space while maintaining accessibility. It is particularly useful for products with a first-in, last-out (FILO) system.
4. Pallet Flow Racking Utilizing gravity, this system allows pallets to flow down an inclined inventory lane. It is best suited for high turnover products and is designed to ensure that the oldest stock is picked first, adhering to the first-in, first-out (FIFO) inventory management principle.
5. Cantilever Racking This type is ideal for storing long or bulky items such as lumber or pipes. The design allows for easy accessibility from both sides, enhancing operational efficiency.
Benefits of Pallet Warehouse Racking
Implementing an efficient pallet racking system presents numerous advantages
pallet warehouse racking
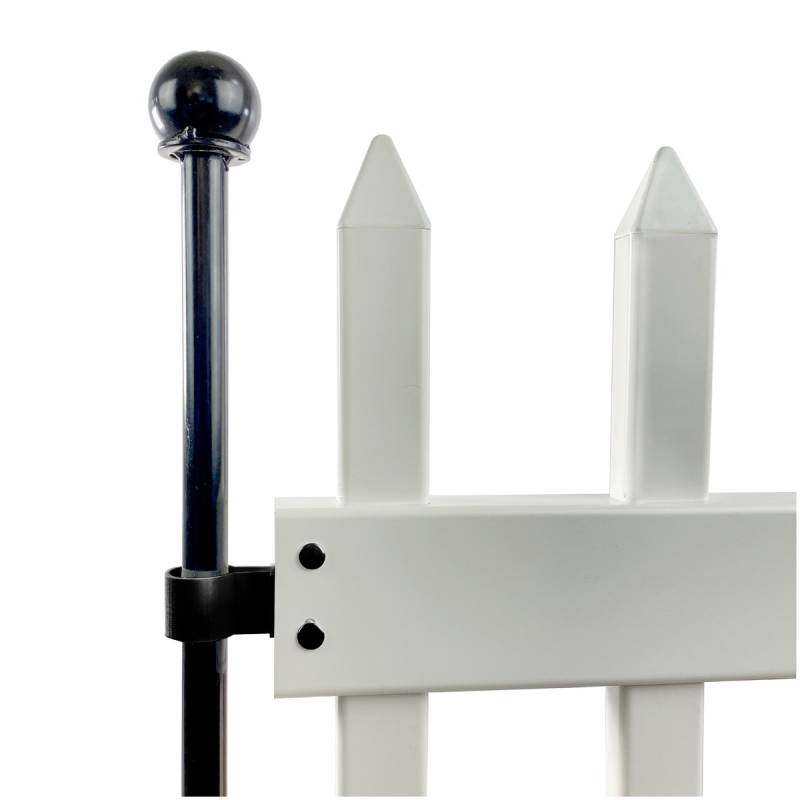
- Maximized Storage Space Racking systems utilize vertical space, allowing for an increase in storage capacity without expanding the warehouse area.
- Improved Accessibility With designated locations for each pallet, employees can easily locate and retrieve products, minimizing time spent searching for inventory.
- Enhanced Inventory Management Racking systems enable better organization of products, facilitating easier stock tracking and inventory turnover.
- Increased Safety Properly designed racking systems can reduce the risk of accidents in the warehouse. Well-distributed weight loads and appropriate aisle widths minimize the chances of forklift collisions and injuries.
- Cost-Effective Operations By optimizing storage space and improving inventory management, pallet racking can lead to significant cost savings in the long run.
Best Practices for Implementation
To reap the full benefits of pallet warehouse racking, consider these best practices
- Assess Your Needs Before selecting a racking system, evaluate the types of products you store, their dimensions, and the expected turnover rates. This assessment will help you select the most suitable racking type.
- Plan Warehouse Layout A well-thought-out layout can significantly enhance operational efficiency. Ensure that aisles are wide enough for forklifts to maneuver safely and access various racking levels with ease.
- Regular Inspections Routine inspections of the racking system are vital to ensure safety and functionality. Look for signs of wear and tear, structural integrity, and compliance with safety standards.
- Training Employees Staff should be adequately trained on best practices for racking systems, including safe loading and unloading procedures, to minimize accidents.
Conclusion
Pallet warehouse racking is fundamental for any warehousing operation looking to optimize space and improve efficiency. By understanding the various types available and implementing best practices, businesses can enhance their logistical capabilities, resulting in improved productivity and customer satisfaction. Investing in the right racking system is not just about organizing space; it’s about supporting the overall operational success of a warehouse.