warehouse shelving cost
Nov . 23, 2024 04:01
Understanding Warehouse Shelving Cost A Vital Aspect of Logistics Management
In today's fast-paced business environment, efficient warehouse management is crucial for the success of any logistics operation. One of the key components of effective warehouse management is shelving, which plays a significant role in organizing products, maximizing space, and ensuring that goods are easily accessible. However, many businesses often overlook the importance of understanding warehouse shelving costs, which can have a substantial impact on their overall operational expenses.
When evaluating shelving costs, it is essential to consider several factors. First and foremost is the type of shelving system chosen. There are various types of shelving available, such as boltless shelving, cantilever shelving, and pallet racking systems. Each type has its own cost implications, installation requirements, and suitability for different warehousing needs. For instance, while pallet racking systems may provide greater vertical space efficiency for bulk storage, they may also require a higher initial investment compared to other systems.
Another significant cost factor is the material used in shelving construction. Shelving can be made from different materials, including steel, plastic, or wood, each with varying price points and durability levels. Steel shelving, for example, tends to be more expensive but offers enhanced strength and longevity, making it a worthwhile investment for warehouses handling heavy loads. On the other hand, plastic or wood shelving may be more affordable initially but could require frequent replacements, leading to higher long-term costs.
warehouse shelving cost
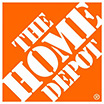
Additionally, the installation and maintenance of shelving systems should be factored into the overall cost. Proper installation is critical for safety and efficiency, and this may require professional assistance, adding labor costs to the total expense. Furthermore, regular maintenance is necessary to ensure the longevity and safety of the shelving, particularly in environments that exhibit wear and tear due to heavy usage or environmental factors.
Space optimization is another crucial aspect that can influence shelving costs. Investing in a shelving configuration that maximizes vertical and horizontal space can substantially reduce the need for additional warehouse space, thereby saving costs in the long run. Conducting a thorough analysis of space requirements and workflow can help businesses choose the most cost-effective shelving systems that align with their operational needs.
Lastly, it is important for businesses to consider the potential for growth. Investing in scalable shelving solutions can lead to significant cost savings if the company expands. Rather than facing the dilemma of complex retrofitting, flexible shelving allows for easy adjustments as inventory levels fluctuate.
In conclusion, understanding warehouse shelving costs is essential for effective logistics management. By evaluating the type of shelving, material choices, installation, maintenance, space optimization, and future scalability, businesses can make informed decisions that align with their operational goals and budget constraints. Investing wisely in warehouse shelving not only enhances efficiency but also contributes to the overall success of the logistics operation.